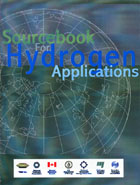
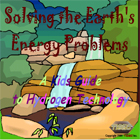
Quick Links
HySTAR™ HyVIEW™ The CH2IP Station | Enter HyVIEW™ Simulation |
About CH2IPMain StationMain Station ConstituentsSatellite StationThe Virtual CH2IP Station |
The CH2IP Station
Main Station Constituents
The main station consists of the following components:
A Stuart Energy Electrolyser designed to generate hydrogen by water electrolysis. The electrolyser, model CF 450-HP, produces hydrogen at a rate of 12 NCMH and has an output pressure of 390 bar (5700 psi). It has a water consumption of 14.6 l/hr.
The following sub-systems are included with the Stuart Electrolyser:- Control panel and rectifier.
- Two Electrolytic Cell Stacks.
- Hydrogen and Oxygen Seals/Demisters.
- Two Hydrogen Compressors (1 duty, 1 stand-by)
- Hydrogen Catalytic purifier.
- Hydrogen Gas Coolers.
- Hydrogen Dryer.
- High Pressure System.
- Condensate Collection System.
- Hydrogen Leak Detection System.
- Heat Detector.
- Cooling Water System.
- Instrument Air System.
- Interconnecting piping, various protective devices and controls for automatic operation.
After the hydrogen is produced, the oxygen is removed from the hydrogen in the catalytic purifier and the hydrogen is then processed through the drying system. The hydrogen exits the electrolyser with a purity of 99.995%. The components enumerated above are integrated in a single package with the dimensions of: 12’11” x 4’10” x 8’6” (LxWxH) and the integrated unit weight is 6000 Kg, and has a power consumption of 80 kW. The power/utilities requirements on the unit are as follows: total power – 130 KVA, voltage – 480 V (AC) ±5%, frequency – 60 Hz/ 3phase. A reliability value for the useful lifetime of the electrolyser cells is about ~ 10,000 hours.
The system employs Dynetek Industries Ltd., hydrogen fuel storage cylinders. The storage system contains sixteen, 438 bar (6350 psi) type 3 cylinders. Each cylinder has a water volume capacity of 150 L and stores approximately 4.25 Kg of compressed hydrogen for a total quantity of 68 Kg of hydrogen available for filling.
Existing CNG fuel system storage cascades are standard DOT 3AA cylinders rated for 250 bar (3600 psi) working pressure, each having a capacity of 20 L (liters). There are 40 cylinders in total and in normal operation they are able to store an approximate quantity of 4 kg of compressed NG for a total of approximately160 Kg of CNG available for filling.
The system employs a hydrogen/CNG blend dispenser manufactured by Fueling Technologies Inc. The dispenser has two filling nozzles, one supplies 100% hydrogen at 350 bar and the second supplies a blend of 50% hydrogen and 50% CNG at 350 bar. The hydrogen/CNG blending is done at the dispenser. First, the dispenser opens the valve to the CNG supply and fills the vehicle with CNG. The CNG supply valve is then closed and the valve to the hydrogen supply is opened and the vehicle is filled with hydrogen. This alternating filling action takes place until the desired fill pressure is reached. Each hose and nozzle assembly for hydrogen and CNG blends are equipped with a breakaway device at the output of the dispenser housing to prevent or minimize the potential possibility of a hazardous event.